Understanding Hydraulic Control, Hydraulic Drive Technology, and Hydraulic Systems
Understanding Hydraulic Control, Hydraulic Drive Technology, and Hydraulic Systems
Blog Article
Hydraulic technology is fundamental to various industrial and engineering applications, providing a means to generate, control, and transmit power through fluid pressure. In this article, we will explore the concepts of hydraulic control, hydraulic drive technology, and hydraulic systems, and how they integrate to create efficient and powerful solutions for a wide range of machinery and equipment.
Hydraulic Systems: The Foundation of Fluid Power
Hydraulic systems are mechanical systems that use liquid (usually oil) to transmit energy from one point to another. The key components of a hydraulic system typically include a pump, motor, valves, fluid reservoir, and various actuators like hydraulic cylinders. These systems are widely used in applications that require precise control of force and movement, such as construction equipment, manufacturing machinery, automotive brakes, and aircraft systems.
Key Components of Hydraulic Systems
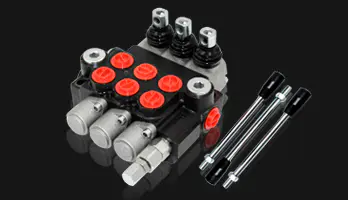
Hydraulic Pump: Converts mechanical energy into hydraulic energy by moving fluid through the system.
Hydraulic Actuators: Includes motors and cylinders that convert hydraulic energy back into mechanical energy to perform work.
Valves: Control the flow, pressure, and direction of the hydraulic fluid.
Reservoir: Stores hydraulic fluid and helps dissipate heat generated within the system.
Hydraulic Fluid: The medium that transmits power throughout the system, typically oil-based for its lubrication and anti-corrosive properties.
Hydraulic systems are prized for their ability to deliver high power in a compact space, providing smooth and controlled operation even under heavy loads. They are essential in industries like manufacturing, construction, agriculture, and transportation.
Hydraulic Control: Precision and Efficiency in Motion
Hydraulic control refers to the techniques and components used to regulate the flow, pressure, and direction of the hydraulic fluid within a system. Control is crucial for ensuring that machinery operates smoothly, safely, and with the desired precision. Hydraulic control systems are responsible for adjusting the speed, force, and direction of movement of the equipment they power.
Types of Hydraulic Control Valves
Directional Control Valves: Direct the fluid to specific pathways within the hydraulic circuit to control the movement of actuators.
Pressure Control Valves: Maintain and regulate the pressure within the system to ensure it operates within safe limits.
Flow Control Valves: Control the speed of the fluid flow, which directly impacts the speed of the hydraulic actuators.
Advanced hydraulic control systems often utilize proportional and servo valves for precise and dynamic adjustments, making them ideal for applications requiring high accuracy, such as robotics, CNC machinery, and aerospace technology.
Hydraulic Drive Technology: Power and Efficiency
Hydraulic drive technology involves the use of hydraulic systems to drive machinery and equipment, converting hydraulic energy into mechanical movement. It is commonly used to produce linear or rotary motion, depending on the application, and is renowned for its ability to deliver immense force with high efficiency.
Advantages of Hydraulic Drive Systems
High Power Density: Hydraulic drives can generate a large amount of power relative to their size, making them suitable for heavy-duty applications.
Smooth Operation: These systems offer smooth and continuous motion, which is essential for applications requiring precise control.
Variable Speed Control: Hydraulic drives can easily adjust speed and torque, providing versatility in operations ranging from slow, powerful movements to fast, delicate motions.
Durability: Hydraulic systems are robust and capable of operating in harsh environments with minimal maintenance requirements.
Hydraulic drive technology is widely used in applications like construction machinery (excavators, loaders), industrial presses, lifting equipment, and marine propulsion systems. Its ability to handle large loads with high precision makes it a preferred choice in various heavy-duty operations.
Integration of Hydraulic Control, Drive Technology, and Systems
The seamless integration of hydraulic control, drive technology, and hydraulic systems forms the backbone of modern machinery and equipment. The success of these systems depends on the precise control of fluid power to achieve the desired mechanical output. When well-designed and properly maintained, hydraulic systems offer unparalleled efficiency, power, and flexibility in industrial applications.
Enhancements with Modern Technology
Modern hydraulic systems have evolved with technological advancements, incorporating digital control systems, sensors, and smart valves that allow for remote monitoring and diagnostics. These innovations enable operators to achieve even greater precision, efficiency, and reliability in hydraulic-powered machinery.
Conclusion
Hydraulic control, hydraulic drive technology, and hydraulic systems together form a powerful trio that drives some of the most demanding machinery in industries worldwide. Understanding how these components work together is crucial for designing efficient systems that deliver precise control, high power, and reliability. With continuous advancements in technology, hydraulic systems are becoming even more versatile, paving the way for innovative solutions in industrial automation, heavy machinery, and beyond.
Check this video:
Report this page